However, to choose one or the other implies to know the particular needs of the buyer.
However, the latest development in the field of full scale appliances is the machining center, which comprises elements and specifications of individual power tools into one singular machine. Until HBJ-16 Micro Boring Bar the 1940s, most industrial manufacturing was based on levers and gears, but soon afterwards, numerical controls (and more recently computer numerical controls) have increased the productivity of these appliances. The high boost in required parts has also altered the way in which power tools are controlled. It is also best to know that while the horizontal machine was highly used before CNC, Boring Head vertical milling machines are far more popular at the moment.
A few examples of very popular machine tools are the drill press, the screw machine, saws, grinding machines etc, but the most common and best known (from before the 1840s) is, of course, the milling machine. The origin of power tools can be traced back to the 1700s, when the need for increased productivity led to the invention of the steam engine. The mass production of machine tools started in the early 19th century and evolved to a point where almost all large or small company has a variaty of distinct appliances.
Even if human or animal power is sometimes (but highly uncommon) used, usually power tools work on one of the three principles: electrical, hydraulic or pneumatic. There are a lot of distinct models of milling machines, but generally they can be found in one of two alternatives: vertical and horizontal (though they vary in size from a normal workbench to a room sized appliance) and their main functions are cutting, planning, drilling etc. The vertical appliance can be lifted or brought down according to need, thus being prefered for heavy industrial manufacturing. Usually, power tools are used for the deformation of metal, but could be used for plastic.
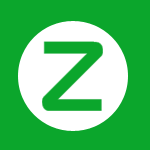